Laser marking technology’s benefits
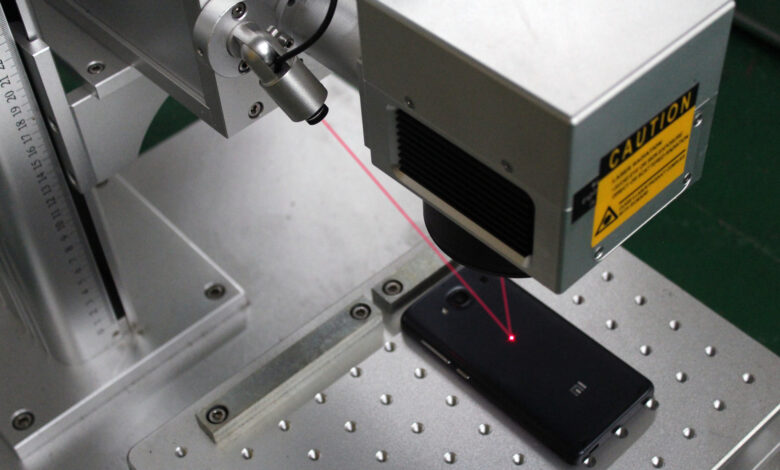
Laser marking of manufactured products is becoming increasingly important in manufacturing. A growing number of businesses keep track of their products to reduce expenses and monitor inventory. Traceability assures manufacturers that suppliers adhere to standard quality requirements, which will improve the quality of their products and reduce recalls and counterfeiting.
But finding the right marking technology for your product and business is easier said than done. Marking technology is a broader category that includes dot peening, laser engraving, inkjet printing, and electrochemical etching. There are pros and cons to each of them, so understanding them before making a choice is crucial. Suppliers typically select a marking method based on some fundamental factors such as type of material, functionality, surface roughness and finish, mark size & dimension, mark quality, coating thickness, and serialization.
The mainstreaming of direct marketing
Manufacturers are using direct part marking, or DPM, to permanently mark parts with serial numbers. This is primarily due to the inability of conventional marking techniques such as stickers to provide full life-cycle tracing. The DPM method is quite popular with manufacturers; specialists use it to identify medical parts. The engraving is usually in the form of alphanumeric characters or barcodes or data-matrix codes. Marking parts with barcodes enables automated post-manufacturing processes such as serial and batch matching or stock database management.
Advantages of laser marking
Generally, laser marking offers several advantages because it is fast and permanent; it also has a lower cost of ownership, doesn’t require additional steps to ensure durability, and uses no consumables, so waste is minimized.
The types of marking technologies
Inkjet Marking
A surface is marked with pressured ink using inkjet marking, also known as “on-the-fly marking.” There are two types of inkjet-based systems: continuous ink jet (CIJ) and drop-on-demand (DOD). In order for the marking to be created, both materials need to be moved. This is a method of creating marks using various nozzles that deposit dots without steering. Array spacing and nozzle spacing determine the size and resolution of the marking. As an alternative, charged ink droplets can be used to create characters with the CIJ method, which is oriented parallel to the material. In the process of moving away from the nozzle, the parts form a dot matrix character.
Electrochemical Etching
Electrochemical etching involves corroding materials with specific chemical and electrical processes. The resulting oxide black surface is the result. The area to be marked must be thoroughly cleaned before marking can begin. The material must then be covered with a mask that has already been produced. The material is then coated with an electrolytic solution.
As the process involves making contact between the electrode and the material, making time may vary from a few seconds to a few hours, depending on the penetration level.
Laser Marking
Laser marking is rapidly replacing the old-fashioned engraving method because it is fast and clean. A laser marking system’s advantages include its ease of automation, its low ownership costs, and its improved environmental profile. Various laser marking systems are available to manufacturers. The characteristics of each type of laser are best suited to a specific application and material. The most common lasers used for universal material marking are carbon dioxide, ytterbium doped fiber, ultraviolet, green, and neodymium vanadate lasers.